NCC New Prefabricated, modular and offsite construction handbook
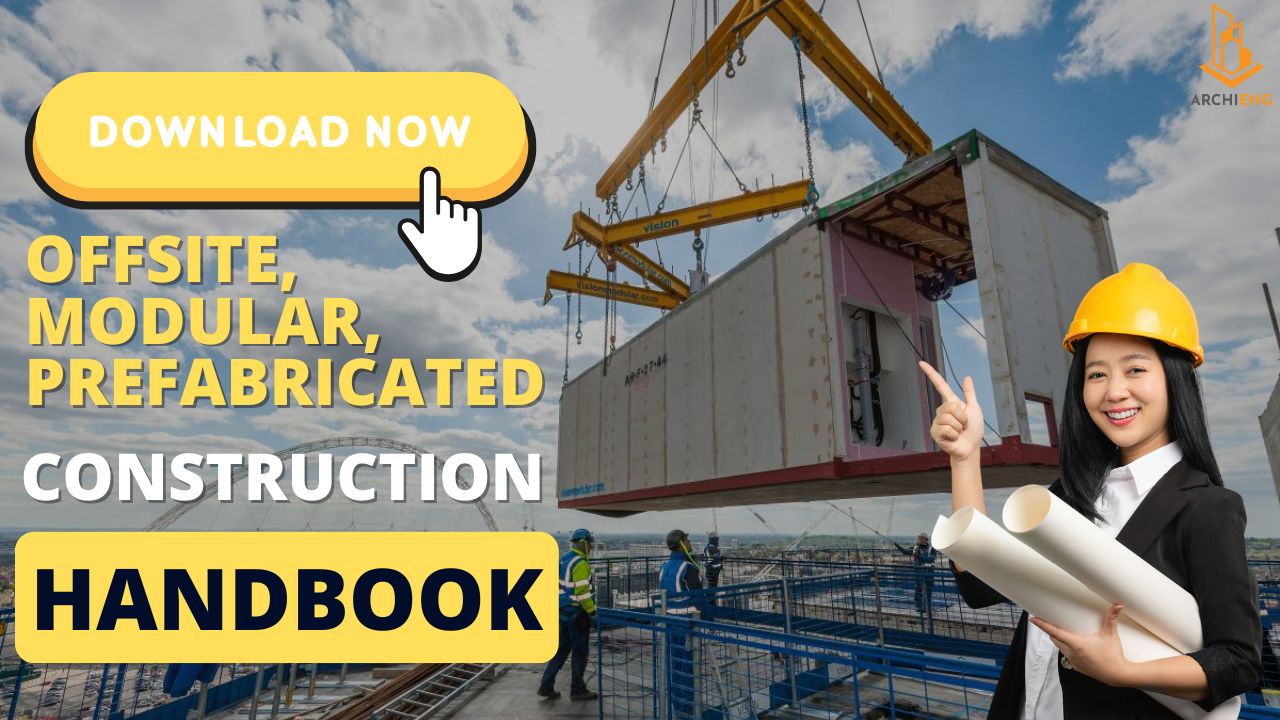
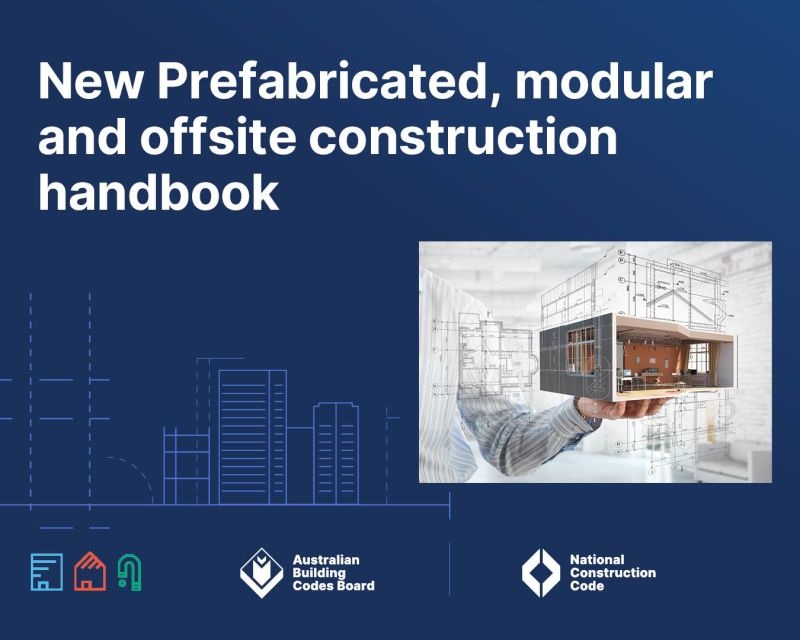
The Australian Building Codes Board (ABCB) has recently released a comprehensive "Prefabricated, Modular, and Offsite Construction Handbook," developed in collaboration with Building 4.0 CRC. This handbook provides essential guidance on utilizing Modern Methods of Construction (MMC) safely, sustainably, and in compliance with the National Construction Code (NCC).
Purpose and Scope of the Handbook
In response to directives from Building Ministers to facilitate the increased use of prefabricated and modular construction to support and expand the supply of new housing, the handbook aims to enhance understanding and application of existing building standards and regulations. It addresses industry and government requests for clear guidance on achieving NCC compliance when employing MMC technologies.
The handbook covers several key areas:
- MMC Systems and Products: An overview of various prefabricated and modular systems, ranging from panelized wall systems to volumetric units like bathroom pods. These systems have the potential to significantly improve construction productivity across all forms of building projects.
- Evidence of Compliance: Guidance on determining the necessary evidence to demonstrate compliance with the NCC, ensuring that all prefabricated and modular constructions meet the required standards.
- Factors Influencing Compliance Outcomes: Identification of critical factors that affect compliance when using MMC, assisting practitioners in navigating the complexities associated with these modern construction methods.
- Integration with Other Resources
The handbook references additional ABCB resources, including the "Evidence of Suitability" and "Performance Solution Process" handbooks, providing a comprehensive suite of guidance materials for practitioners. These resources collectively support the effective implementation of MMC technologies in compliance with the NCC.
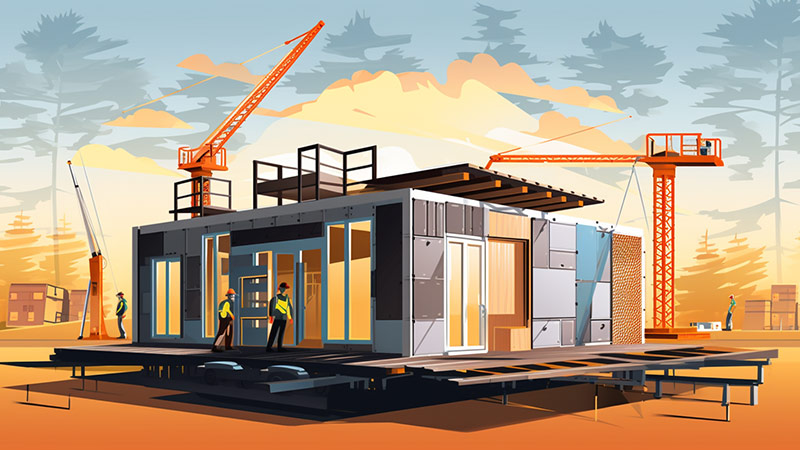
Implications for the Construction Industry
The release of this handbook is a significant step toward modernizing construction practices in Australia. By promoting the use of prefabricated and modular systems, the industry can achieve:
- Increased Productivity: Offsite manufacturing and modular construction can reduce construction times and improve efficiency, as demonstrated by recent projects like the seven-storey apartment block in Brisbane, which was erected in just 11 days using prefabricated components.
- Enhanced Quality Control: Manufacturing components in controlled environments allows for better quality assurance and adherence to standards.
- Sustainable Building Practices: MMC technologies can contribute to more sustainable construction methods by minimizing waste and optimizing resource use.
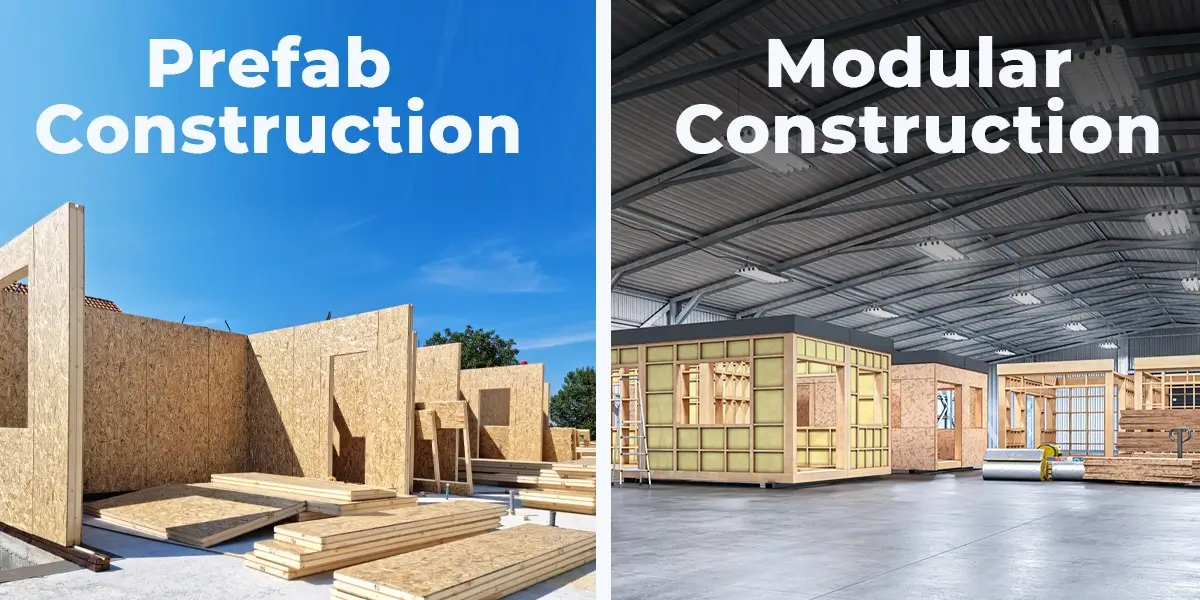
What's the difference between Prefabricated and Modular Construction
Prefabricated construction and modular construction are closely related terms, but they refer to different methods of building and have unique characteristics. Here’s a breakdown of the differences:
1. Prefabricated Construction
Definition:
Prefabricated construction involves manufacturing building components or assemblies in a factory or controlled environment and then transporting them to the construction site for assembly.
Key Features:
- Components: Prefabrication typically involves individual building components, such as walls, floors, roofs, or structural steel members, being produced offsite.
- Assembly on Site: These components are shipped to the construction site and assembled to create the final structure.
- Flexibility: Prefabricated elements can be used in a variety of construction projects, including traditional site-built and modular buildings.
- Examples: Precast concrete panels, steel trusses, timber frames, and cladding systems.
Advantages:
- Faster construction due to simultaneous site preparation and component manufacturing.
- Improved quality control from factory production.
- Reduced material waste and environmental impact.
Limitations:
- May require significant on-site assembly.
- Components must fit precisely to avoid delays.
2. Modular Construction
Definition:
Modular construction is a subset of prefabricated construction where entire building modules or sections are manufactured offsite and then transported to the site for installation.
Key Features:
- Fully Built Modules: Modular construction involves creating whole volumetric sections (e.g., rooms, apartments) complete with finishes, plumbing, and electrical systems.
- Minimal Site Work: Once transported to the site, the modules are joined together, making the final assembly quicker than prefabrication.
- Standardization: Modules are often standardized, making this method particularly suited for repetitive designs like hotels, apartment complexes, or hospitals.
- Examples: Fully constructed bathroom pods, kitchen units, or entire apartment units.
Advantages:
- Significantly faster construction timelines due to minimal on-site work.
- High quality and consistency due to factory production.
- Modules can be designed for future disassembly and reuse.
Limitations:
- Transportation of large modules can be challenging and costly.
- Limited customization after module fabrication.
Key Differences
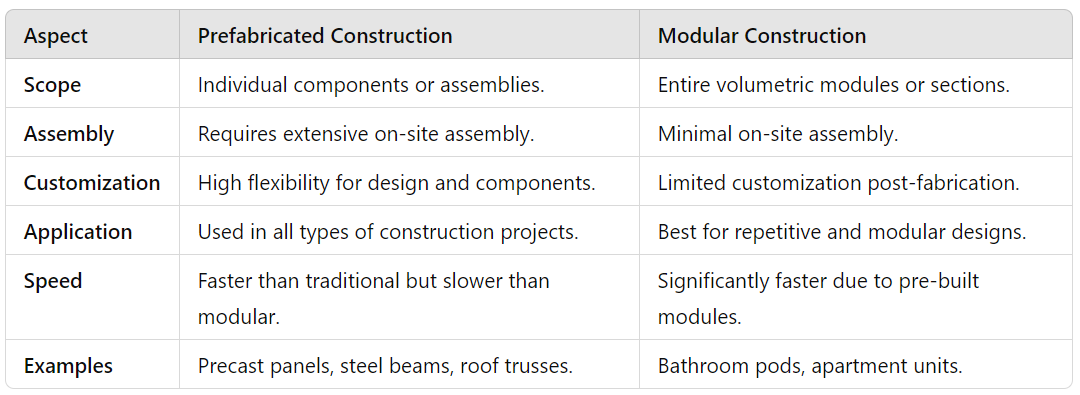
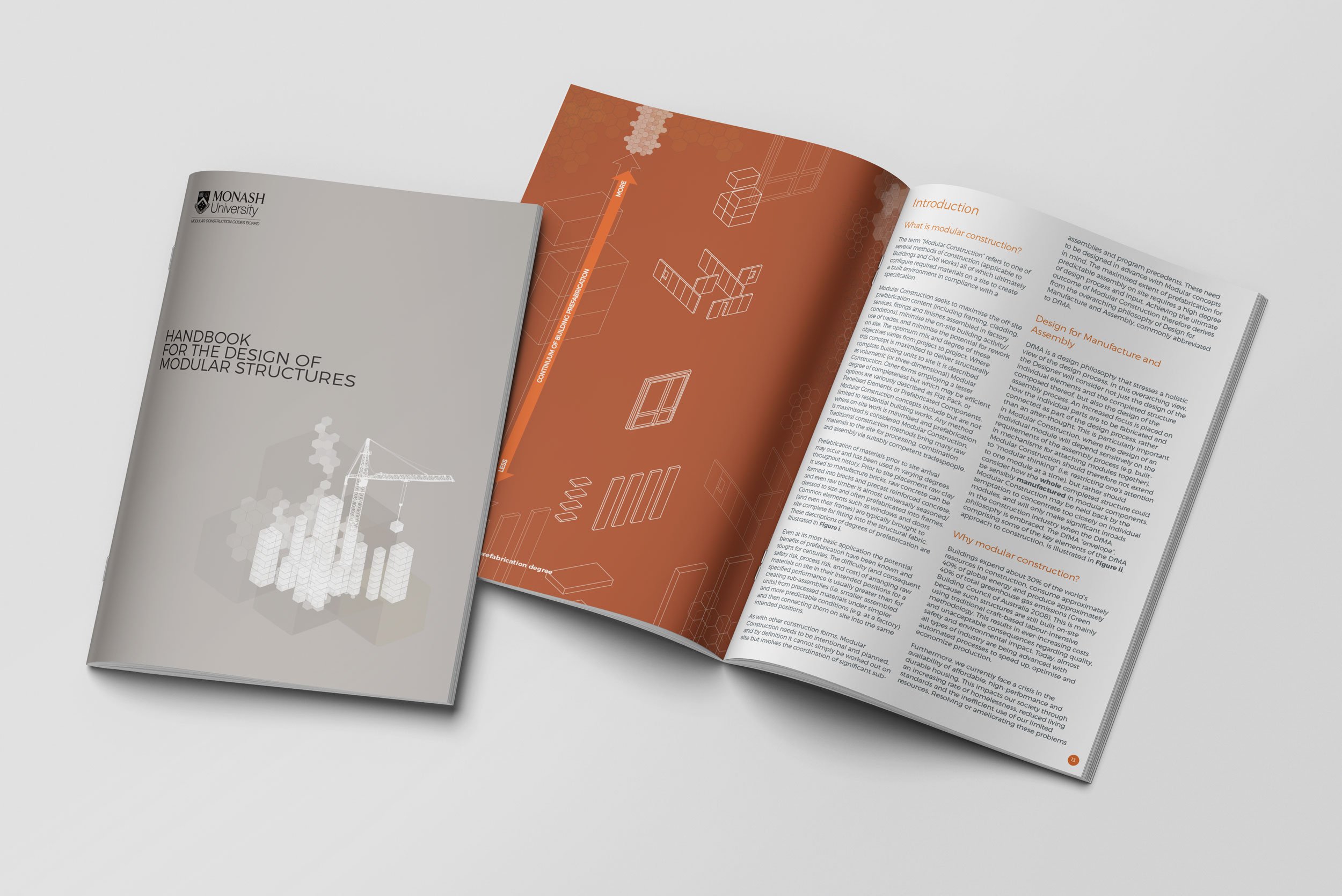
Monash University - Handbook For The Design of Modular Structures
This handbook was initially instigated by Prof. James Murray-Parkes, Prof. Yu Bai, Adam Styles, Angela Wang, Monash University, the Victorian Government, and various industry partners.
This handbook was the first of its kind in the world, providing integrated solutions and experiences to industry, government and the community including: Design for performance; Design for Manufacture and Assembly (DfMA); and Regulatory compliance. The Handbook is a project by the Modular Construction Codes Board (MCCB) to provide guidance to the industry on the design and construction of modular structures.
The aim of the Handbook is to share the experience and knowledge advances in modular manufacturing and construction for improving safety, productivity and quality in industrial practices. It is intended that this Handbook be an evolving document, to be reviewed by a larger community of technical professionals and organizations, both in Australia and world-wide.
Conclusion
The ABCB's "Prefabricated, Modular, and Offsite Construction Handbook" and Monash University "Handbook For the Design of Modular Structures" are invaluable resources for industry professionals seeking to adopt modern construction methods in compliance with national standards. By providing clear guidance and referencing supplementary resources, the handbook supports the industry's transition toward more efficient, sustainable, and innovative building practices.
Prefabricated construction Prefabricated building components Prefabrication techniques Offsite construction methods Prefabricated homes Precast concrete panels Prefabricated steel structures Timber prefabrication Prefab construction benefits Prefabricated roof trusses Prefab vs traditional construction Prefabrication process Modern prefabricated designs Prefab housing solutions Sustainable prefabrication Prefab construction challenges Prefabrication and building codes Prefabricated cladding systems Prefabricated wall systems Advantages of prefabrication Prefab structural elements Prefabricated schools Prefab for residential buildings Prefabricated commercial buildings Prefab materials History of prefabrication Prefab manufacturing process Prefab modular hybrid systems Prefabricated transport logistics Prefabrication in high-rise buildings Prefab cost savings Prefabricated infrastructure Prefabricated construction trends Prefab in sustainable architecture Prefabricated housing innovations Factory-built construction components Prefab project case studies Prefabricated building lifecycle Prefab construction durability Prefab energy efficiency Prefabricated disaster relief shelters Prefabricated green buildings Prefab construction productivity Prefabrication and worker safety Prefab installation techniques Prefabrication in urban development Prefab for remote locations Prefabricated insulation systems Modular prefab integration Prefab 3D printing technology Modular construction Modular building systems Modular homes Modular construction process Modular building designs Modular housing solutions Volumetric modular construction Modular construction benefits Modular construction challenges Modular apartments Modular office buildings Modular vs prefabricated construction Modular building codes Modular construction for hospitals Modular school buildings Modular construction trends Modular construction cost Modular bathroom pods Modular kitchen units Sustainable modular buildings Prefab modular combination Modular building lifecycle Modular construction in urban areas Modular building materials Modular project case studies Future of modular construction Modular construction in data centers High-rise modular construction Modular construction factories Modular construction logistics Modular residential buildings Modular commercial spaces Modular construction speed Custom modular designs Standardized modular units Modular building flexibility Modular healthcare facilities Modular hotel construction Modular construction technology Modular eco-friendly construction Reusable modular buildings Modular construction durability Modular temporary structures Modular workforce housing Modular construction in Australia Modular shipping container homes Modular construction for disaster recovery Modular 3D printing Modular design for efficiency Modular construction innovations